Transformer accidents happen from time to time and there is a growing trend. From the analysis of transformer accidents, the short-circuit-tolerance capability has become the leading cause of power transformer accidents, causing great harm to the power grid and seriously affecting the safe operation of the power grid.
The following accidents often occur in transformers: external multiple short-circuit shocks, the coil deformation is gradually serious, the final insulation breakdown damage; the external short-term impact of short-term frequent damage; a long-term short-circuit shock damage; a short-circuit shock damage. The main forms of transformer short-circuit damage are the following:
1, axial instability. This damage is mainly caused by the axial electromagnetic force generated by radial leakage magnetic flux, resulting in axial deformation of the transformer windings.
2, line cake up and down bending deformation. This damage is due to the fact that the wire between the two axial pads under the action of the axial electromagnetic force causes permanent deformation due to excessive bending moments, usually the deformation between the two cakes is symmetrical.
3, winding or line cake collapsed. This damage is due to the wire squeezing or impacting each other under the action of an axial force, resulting in an oblique deformation. If the wire is slightly tilted, the axial force will increase the tilt and collapse when it is severe. The larger the ratio of height and width of the wire, the easier it will be to cause the collapse. In addition to the axial component of the end leakage magnetic field, there is also a radial component. The resultant electromagnetic force generated by the magnetic leakage in the two directions causes the inner winding wire to turn inward and the outer winding to turn outward.
4, the winding rises to open the pressure plate. This damage is often due to excessive axial forces or the presence or lack of strength of their end supports, insufficient rigidity or assembly defects.
5, instability of the radial direction. This damage is mainly caused by the radial electromagnetic force generated by axial magnetic flux leakage, resulting in radial deformation of the transformer windings.
6, the elongation of the outer winding leads to insulation damage. The radial electromagnetic force attempts to increase the diameter of the outer winding. When the tensile stress acting on the wire is too large, permanent deformation occurs. This deformation is usually accompanied by damage to the conductor insulation resulting in a short circuit between the turns. In severe cases, it can cause the coil to jam in, chaos, collapse, and even break.
7, the winding end turn deformation. In addition to the axial component of the end leakage magnetic field, there is also a radial component. The resultant electromagnetic force generated by the magnetic leakage in the two directions causes the winding wire to turn inward and the outer winding to turn outward.
8. The inner winding wire is bent or bent. The radial electromagnetic force reduces the diameter of the inner winding, which is the result of a permanent deformation caused by excessive bending moments of the wires between the two supports (internal stays). If the iron banding is sufficiently tight and the winding spokes are effectively supported by the struts, and the electric power is distributed evenly in the circumferential direction from the spokes, the deformation is symmetrical and the entire winding is a multi-sided star. However, due to the deformation of the iron core, the supporting conditions of the strut are not the same, and the force along the circumference of the winding is not uniform. In fact, local instabilities often occur to form warping deformation.
9, lead fixed instability. This damage is mainly caused by the electromagnetic force between the leads, causing the leads to vibrate, resulting in a short circuit between the leads.
Transformer short circuit fault analysis:
There are many reasons for transformer internal faults and accidents due to transformer outlet short circuit, and it is also more complicated. It is related to structural design, quality of raw materials, technological level, operating conditions and other factors, but the selection of electromagnetic wire is the key. In recent years, the electromagnetic wire selected based on the transformer static theory design has been widely used in the anatomy and voltage transformation, and the stress acting on the electromagnetic wire during actual operation has a great difference.
(1) At present, the calculation procedures of various manufacturers are based on idealized models such as uniform distribution of leakage magnetic field, the same diameter of turns, and equal phase forces. However, in fact, the leakage magnetic field of the transformer is not evenly distributed. Relatively concentrated in the iron yoke portion, the area of ​​the electromagnetic wire is subject to greater mechanical force; transposition of the wire in the transposition due to climbing will change the direction of transmission of force, resulting in torque; due to the modulus of elasticity of the cushion, the shaft Unequal distribution to the spacer will cause the alternating force generated by the alternating leakage magnetic field to delay resonance, which is why the first line deformation of the line cake is located at the yoke part of the core, the transposition part, and the corresponding part of the pressure regulation tap. The root cause.
(2) The effect of temperature on the bending and tensile strength of the magnet wire was not considered when calculating the ability to withstand short-circuits. The short-circuit resistance designed at room temperature does not reflect the actual operation. According to the test results, the temperature of the magnet wire has a great influence on its yield limit 0.2. With the increase of the temperature of the magnet wire, its bending strength, tensile strength and elongation rate Both decreased, the bending strength at 250°C decreased compared with that at 50°C, and the elongation decreased by more than 40%. The actual operation of the transformer, under rated load, the average winding temperature up to 105 °C, the hottest point temperature up to 118 °C. Normally, the transformer is re-closed during operation, so if the short-circuit point cannot be eliminated for a short time, it will be followed by a second short-circuit shock in a very short time (0.8s), but due to the impact of the first short-circuit current, The temperature of the winding increases sharply. According to the provisions of GBl094, the maximum allowable temperature is 250°C. At this time, the short-circuit resistance of the winding has been greatly reduced. This is why most of the short-circuit accidents occur after the reclosing of the transformer.
(3) The use of ordinary transposed conductors, poor resistance to mechanical strength, when subjected to short-circuit mechanical force prone to deformation, loose strands, exposed copper phenomenon. When using common transposed conductors, due to the large current, the steep slope of the transposition will produce a large torque at this part, and at the same time, the line cakes at the two ends of the windings will also produce a combination of axial and axial leakage magnetic fields. Larger torque causes distortion. For example, Yang Yang's 500 kV transformer has a total of 71 transpositions in the A-phase common winding. Due to the use of thicker common transposed conductors, 66 transpositions have varying degrees of deformation. In addition, the No. 1l main change of Wusong is also due to the phenomenon that the high-voltage winding two-end line cake in the yoke part of the iron core has different flipping dew lines due to the use of ordinary transposing wires.
(4) The use of soft wires is also one of the main reasons for the poor resistance of transformers to short circuits. Due to the lack of early understanding of this, or the difficulty of winding equipment and processes, manufacturers are reluctant to use semi-rigid wire or no requirements in this regard at the time of design. From the point of failure of the transformer, they are all soft wires.
(5) winding winding loose, improper transposition processing, too thin, resulting in electromagnetic wire hanging. From the point of view of accident damage, deformation is more common at the transposition, especially at the transposition of the transposed conductor.
(6) Uncured winding turns or wires have poor resistance to short circuits. None of the early dip-lacquered windings were damaged.
(7) Improper control of the pre-tightening force of the windings causes misalignment of the conductors of common transposed conductors.
(8) The set clearance is too large, resulting in insufficient support on the electromagnetic wire, which increases the potential for the transformer to withstand short-circuit.
(9) The effect of uneven preload on the windings or the various stages, the line cake's beating caused by the short-circuit impact, resulting in the bending stress acting on the electromagnetic wire is too large and deformation occurs.
(10) Frequent external short-circuit accidents, accumulation of electromotive forces after multiple short-circuit current surges cause the magnet wire to soften or internal relative displacement, eventually leading to insulation breakdown.
Transformer short-circuit damage common parts
Corresponds to the part under the yoke. The causes of deformation at this location are: (1) The magnetic field generated by the short-circuit current is closed by the oil and the wall or iron core. Because the magnetic resistance of the iron yoke is relatively small, most of the magnetic resistance is closed by the oil circuit and the iron yoke, and the magnetic field is relatively concentrated. The electromagnetic force acting on the online cake is also relatively large; (2) the inner winding set gap is too large or the iron core binding is not tight enough, resulting in shrinkage of the two sides of the iron core sheet, resulting in warping deformation of the iron yoke side winding; (3) in the structure The axial compression of the yoke part corresponding to the winding part is the least reliable, and the line cake of this part is often difficult to achieve the pre-tightening force, so the line cake at this part is most easily deformed.
Pressure tapping area and corresponding to other windings. This region is due to: (1) Imbalances in the ampoules that make the magnetic flux distribution unbalanced, and that the additional leakage magnetic field in the amplitude creates additional axial external force in the coil. The direction of these forces always increases the asymmetry of these forces. Big. The axial external force and the normal internal force generated by the normal amplitude to the magnetic flux leakage cause the linear cake to bend in the vertical direction and compress the cushion pieces of the wire cake. In addition, these forces are partially or completely transmitted. On the iron yoke, trying to make it out of the heart column, the phenomenon that the line cake is deformed or turned to the middle of the winding. (2) The line cakes in this area are intended to have an insulation distance between the ampoules or the tapping zone. It is often necessary to increase the number of pads, and the thicker pads will cause a delay in the transmission of force, and thus impact on the line cake. Larger; (3) The height alignment of the center reactance cannot be ensured after the winding is set, resulting in further exacerbation of the imbalance of the ampoule; (4) After a certain period of time, the thicker pad naturally shrinks, which on the one hand increases the imbalance of the ampoule. Phenomenon, on the other hand, increased jitter when subjected to a short-circuit force; (5) In order to balance the stability of the ampoule during the design time, the electromagnetic wire in the tapping zone was selected with a narrow or small cross-section wire gauge, and the resistance to short-term force was low.
Transposition site. This part of the deformation is common in the transposition of the transposed conductor and the standard transposition of the single helix. Transposition of the transposing wire, because of the steeper displacement of the transposed conductor than that of the ordinary conductor, the opposite tangential force is generated at the transposition where the radius of the raft differs. This is the opposite direction of the tangential force, As a result, the diameter of the inner winding is reduced and the direction is distorted. The commutation force of the outer winding is the same as the radius of the turn, so that the straightening is performed, the inner lining is deformed toward the center, the outer lining is outwardly deformed, and the wire thickness is exchanged. The thicker the steeper the climb, the more severe the deformation. In addition, there is an axial short-circuit current component at the transposition, resulting in additional force, resulting in increased deformation of the strand cake. The standard transposition of a single helix occupies a single position in space, resulting in an unbalanced ampoule at the site. At the same time, it has the transposition and transposition deformation characteristics of the transposition wire, so the line cake at this site is more easily deformed.
The lead of the winding. It is common in windings with oblique helical structure. The windings of the structure, due to the imbalance of the two spiral mouths, the axial force is large, and the axial current is also present, causing a lateral force at the corner of the lead line to be distorted. phenomenon. In addition, during the winding process of the spiral winding, there is residual stress, which will cause the winding to strive to restore the original state, so the winding of the spiral structure is more easily deformed under the impact of the short-circuit current.
Leads. Commonly used between low-voltage leads, the low-voltage lead has a large current flowing through the voltage and is 120 degrees in phase, making the leads attract each other. If the leads are not properly fixed, a short circuit between the phases occurs.
Pedal Bin
Pedal Bin
1. Hands-free opening with a foot pedal to prevent the spread of germs.
2 The stainless steel body of the bin is fingerprint-proof, smudge-resistant, and easy to clean.
3.Perfect way to store trash in your kitchen, office, wherever space is limited .
4. Inner compartments are removable and holds much crash.
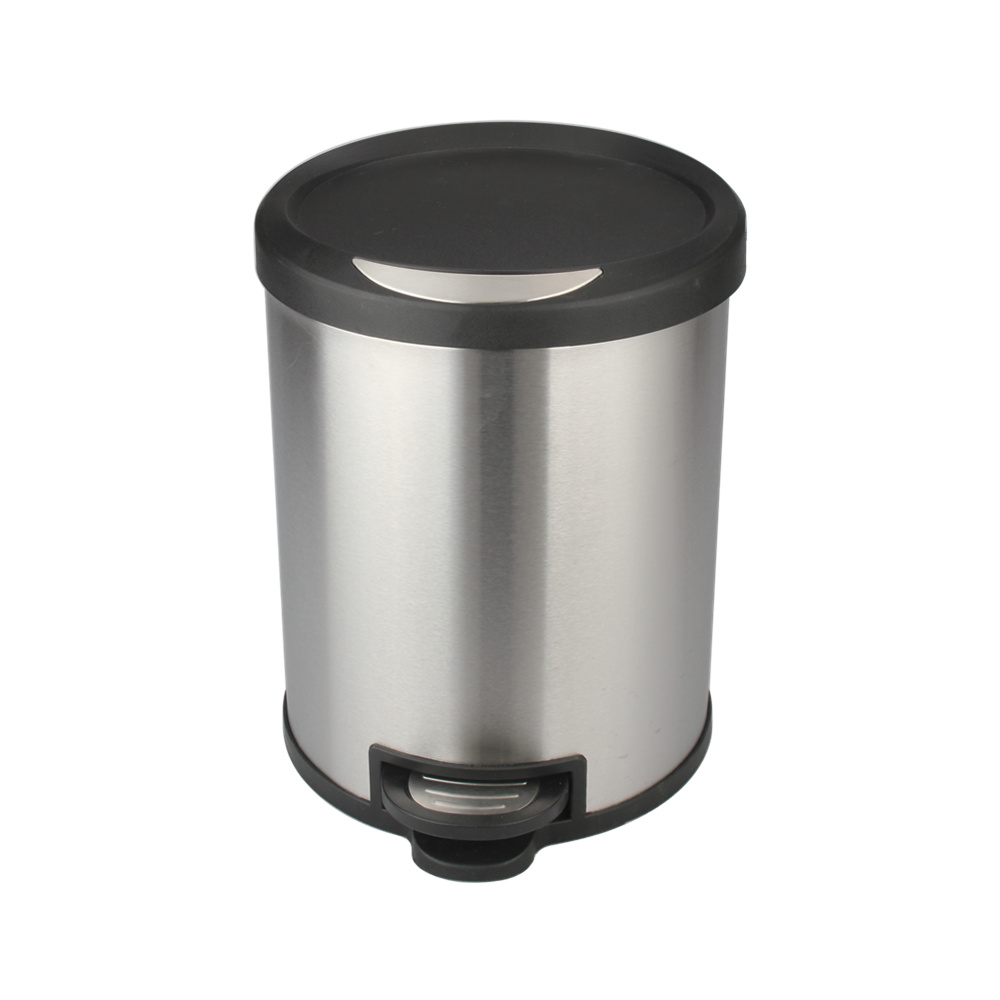
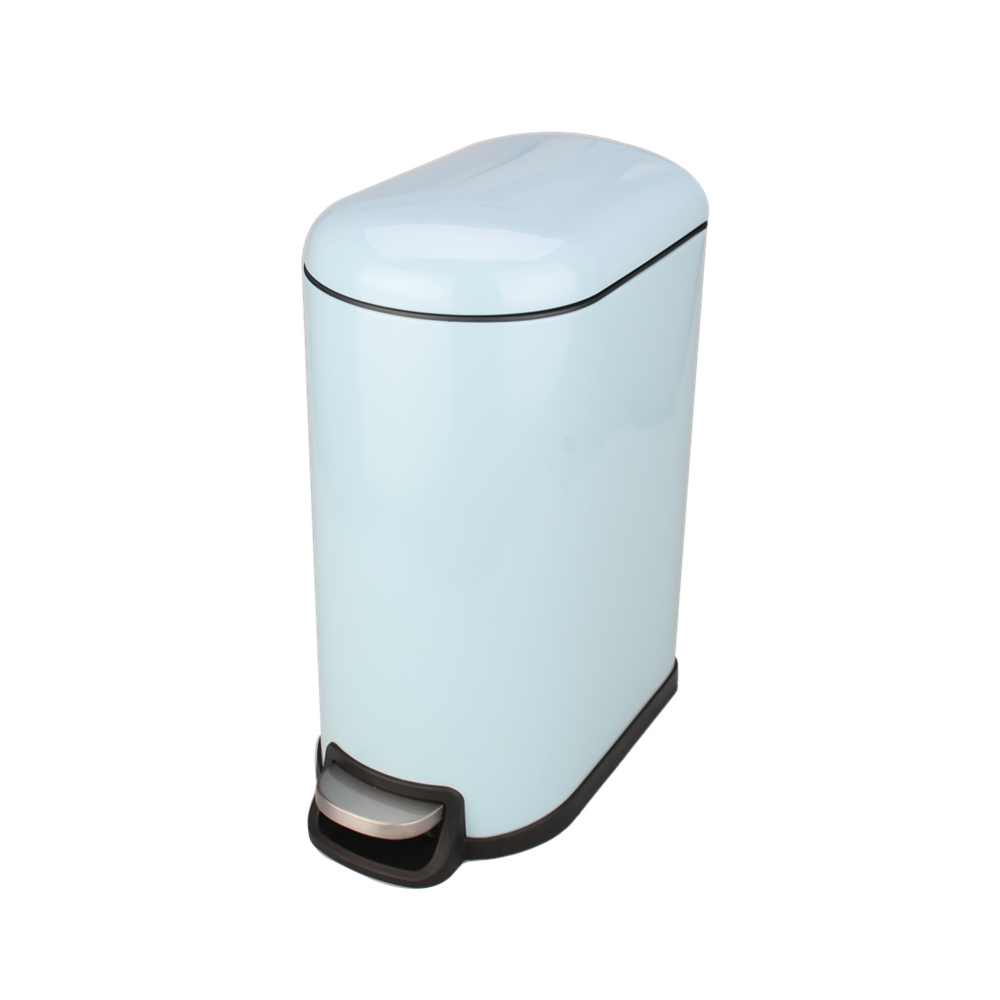
FAQ:
1:How can
I get the sample?
We can
provide the sample for customers to check the quality.
Please
kindly provide the delivery info for calculate the sample cost. If you have DHL
/TNT/UPS/FEDEX account, please also kindly provide it to us.
You can
do the payment of sample via T/T and PayPal.
2:How
about the sample time?
Usually
the sample time is 7~10 days after have the sample cost.
3:How
long will it take for mass production?
Usually
45~60 days after have the deposit.
4:Can we
have our logo or company name to be printed on your products or the package?
Welcome
OEM.
5:what
certificate can you provide?
CE,CB,GS,FDA,LFGB,ROHS
are available here.
6:How can
we get your monthly new products announcement?
Please join our mailing lists.